Challenges and opportunities in semiconductor fab planning and construction
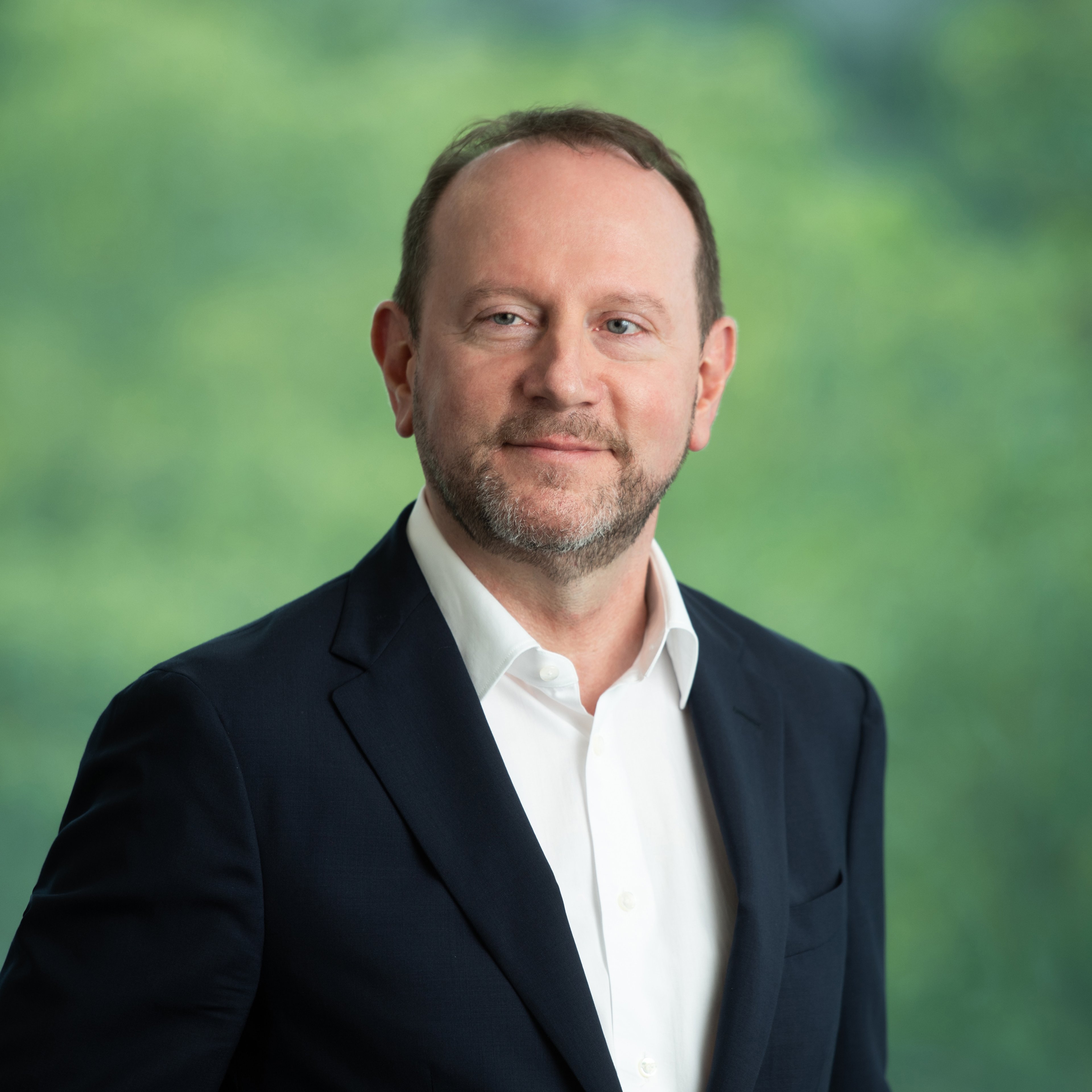
Challenges and opportunities in semiconductor fab planning and construction
Herbert Blaschitz, Executive Vice President and Chief Technology Officer at Exyte, discusses the challenges of constructing semiconductor fabrication plants (commonly referred to as “fabs”) in the U.S. compared to Taiwan. He highlights that building such facilities in the U.S. can be twice as expensive and take twice as long due to factors like complex regulatory processes and a less experienced workforce. To address these challenges, Blaschitz suggests adopting “virtual commissioning” which involves creating a digital model of the plant before physical construction begins. This approach allows potential issues to be identified early, as well as adding new technologies, thereby reducing costs and environmental impact while improving efficiency.
Taiwan: A benchmark for speed and cost efficiency
In terms of cost, fab construction in the West is at least 50 percent more expensive than in Asia for similar sized and technologically comparable fabs. The higher costs stem primarily from construction including materials, labor (especially skilled trades and engineering), site preparation and utilities infrastructure, and permitting and regulatory requirements, Blaschitz specifies. However, since over 80 percent of a fab’s total capital expenditure is allocated to equipment, which remains relatively similar across regions when excluding factors such as taxation, subsidies, or grants, the difference in construction costs results in the overall fab investment to be approximately 20 percent higher in the West than Asia.
Taiwan continues to set industry benchmarks for speed and cost efficiency. On average, it takes just 19 months to build a fab from permitting and design to handover. Additionally, Taiwan leads in fab decarbonization, demonstrating a strong commitment to sustainability measures in their facilities.
Virtual commissioning: Reducing operating costs and carbon footprint at the same time
To remain competitive, chipmakers seek sustainability initiatives that also provide cost and schedule benefits. Blaschitz introduces Exyte’s virtual commissioning, one of the latest innovations developed by the company as an opportunity to bring added value to the client. Driven by dynamic energy and scheduling modeling, virtual commissioning enables predictive and highly precise calculations of a fab’s energy and water consumption, along with its corresponding carbon emissions. "Since this analysis is conducted during the fab design phase, it enhances predictability and allows fab owners to take proactive measures, thereby improving decision-making well before construction begins," Blaschitz says. Furthermore, simulating different scheduling scenarios allows for effective planning and monitoring.
In Germany, virtual commissioning was successfully used to optimize the design and planning of a mega fab, resulting in significant energy savings. These savings will translate to an annual reduction of tens of thousands of tons in carbon emissions and millions of dollars in operating cost savings including lower carbon emission taxes. Furthermore, this digitalized fab engineering solution is cost-effective with a return on investment of less than six months, depending on the scale of the fab, Blaschitz points out.
Labor challenges: Availability and talent gap remain key issues
The speed at which new fabs are required to be built to meet the semiconductor demand in such a short timeframe is unprecedented. Moreover, the rapid influx of new fab investments in the West further exacerbates labor constraints, not only to operate these facilities but to construct them as well. According to SEMI, more than 60,000 chip design and manufacturing jobs are expected to remain unfilled until 2030 in the U.S. alone. Additionally, a similar number of fab construction workers will be needed through the end of the decade.
“Fab owners need to prioritize early planning and decide to build ahead of demand, before everyone else, to avoid competing in an already tight labor market,” Blaschitz advises. Increased automation and the use of robotic equipment will also help mitigate labor constraints.
While improvements to government policies can certainly benefit the industry, Blaschitz emphasizes the need for continuous innovation, increased collaboration, and greater adaptability. The long-term goal remains clear: Reduce costs, increase productivity, and accelerate fab construction timelines.
ARE YOU LOOKING FOR :
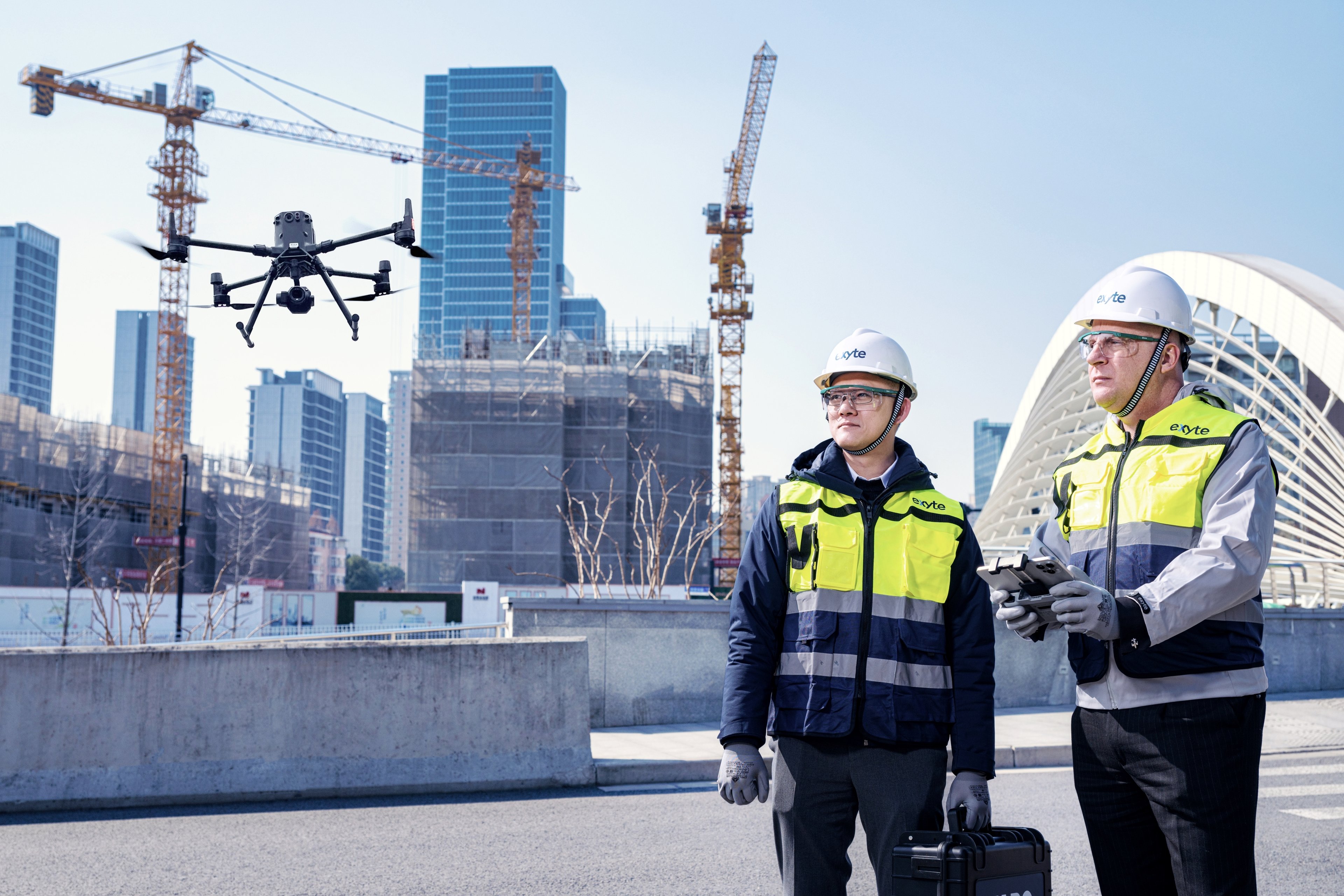
Innovation and Expertise
/201203PHOBLSPharma7-1dark.jpg?w=3840)
People and Stories
.jpg?w=3840)
About us
ARE YOU LOOKING FOR :
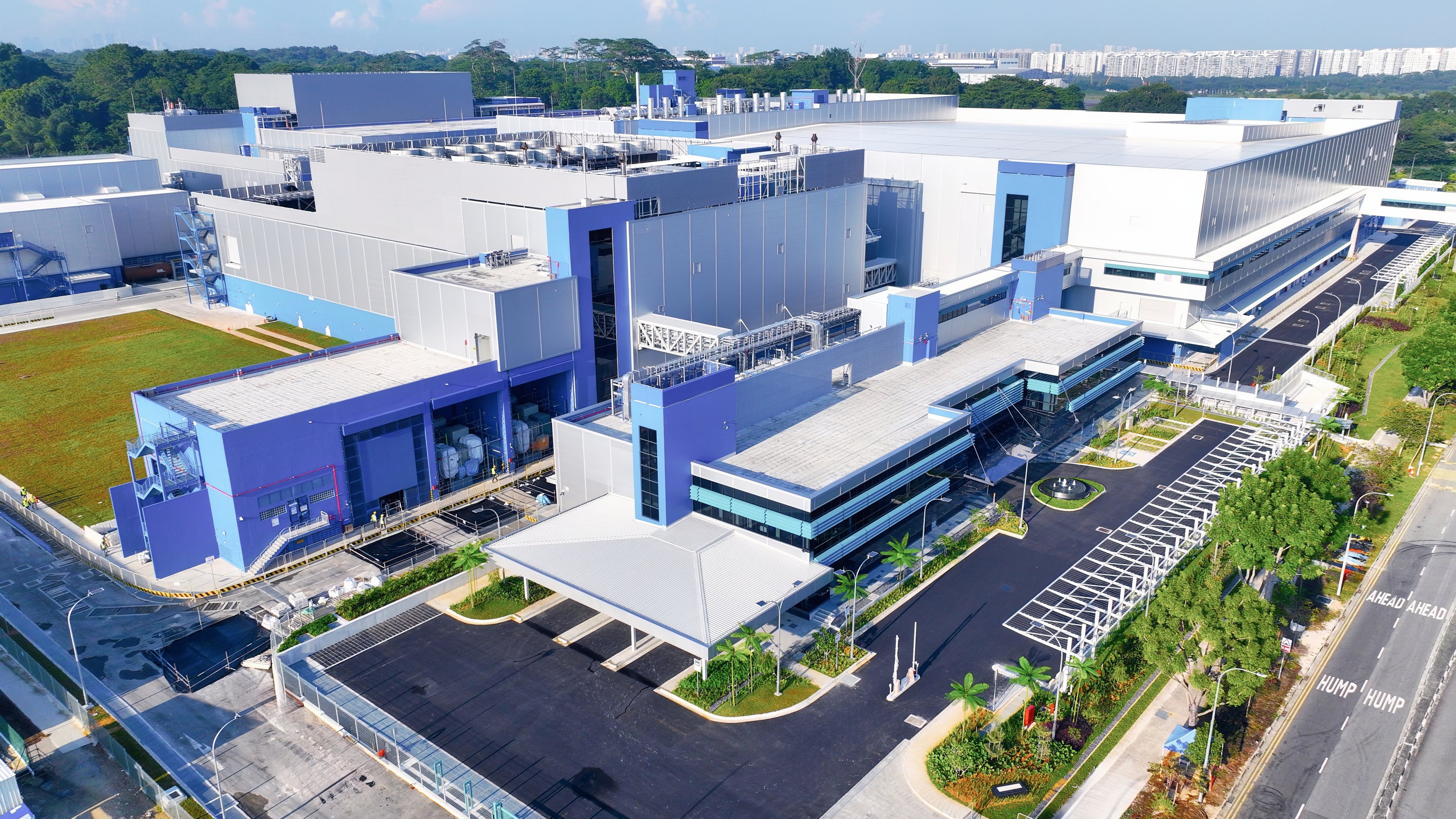
Projects
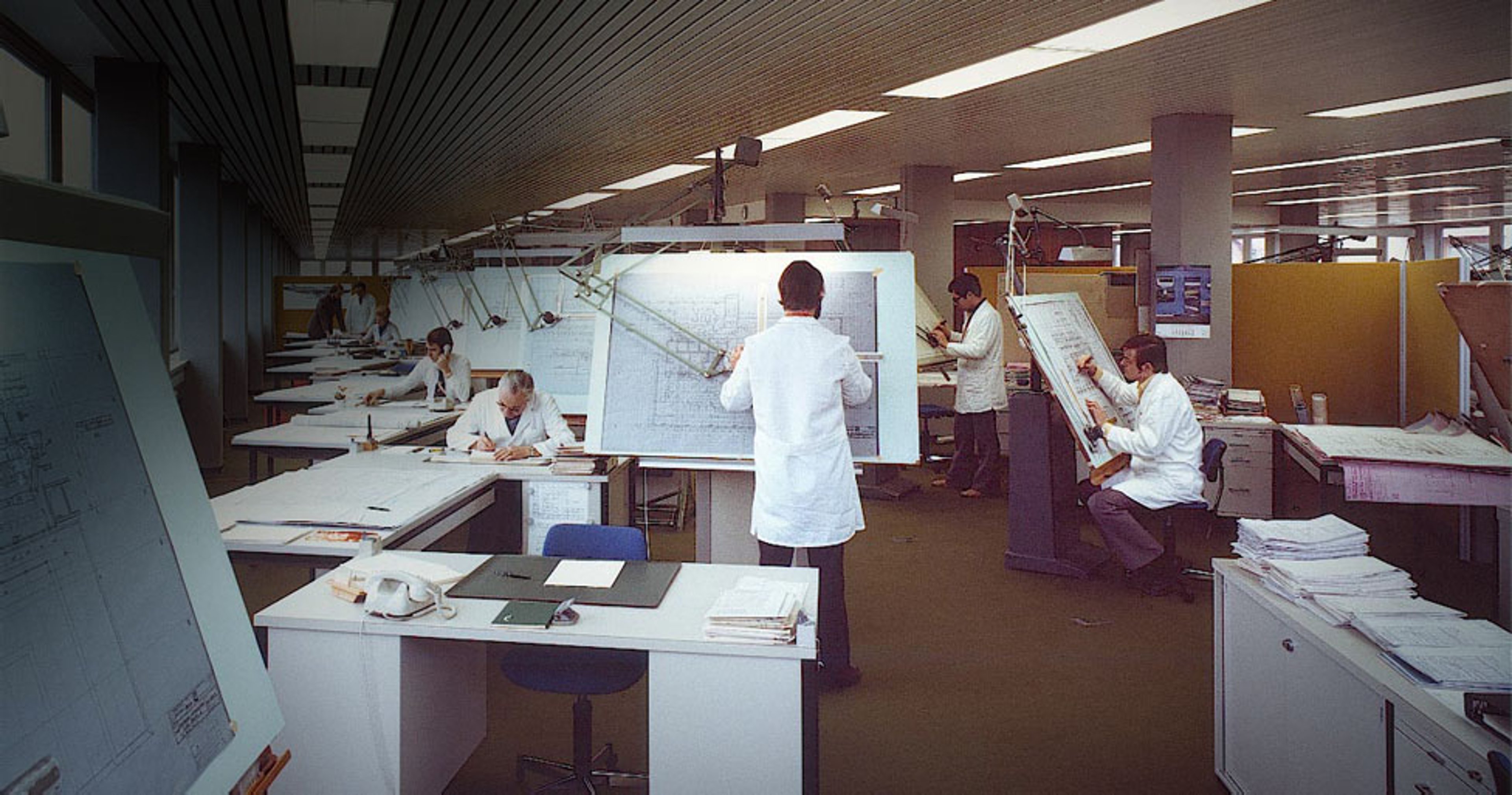